
Researchers report three-D printed latex rubber step forward
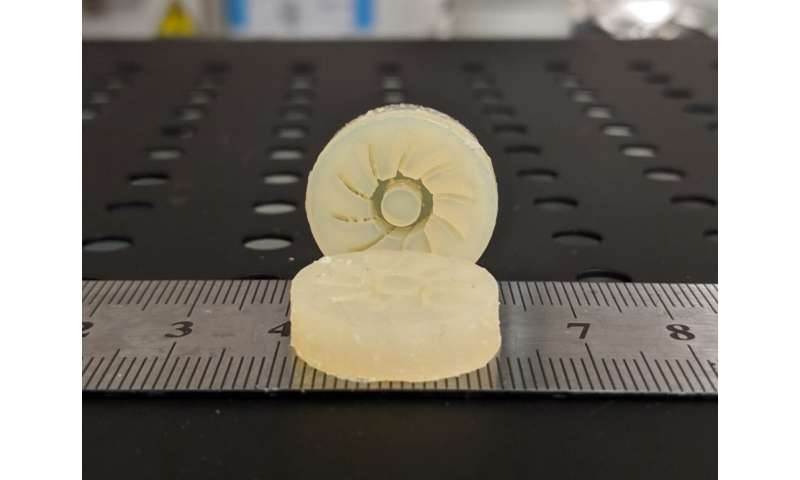
Virginia Tech researchers accept as true with chanced on a weird course of to a pair of-D print latex rubber, unlocking the skill to print a fashion of elastic materials with complex geometric shapes.
Latex, many times identified as the materials in gloves or paint, refers to a neighborhood of polymers—prolonged, repeating chains of molecules—coiled inner nanoparticles dispersed in water. three-D printed latex and a fashion of equally rubbery materials called elastomers would possibly maybe well well be former for a fashion of applications, including soft robotics, scientific devices, or shock absorbers.
three-D printed latex has been documented top probably a handful of instances in scientific literature. None of the outdated examples come end to the mechanical properties of the latex printed by an interdisciplinary team affiliated with the Macromolecules Innovation Institute (MII), the College of Science, and the College of Engineering.
By unusual innovations in every the chemistry and mechanical engineering disciplines, the team overcame some prolonged-standing obstacles of three-D printing, additionally identified as additive manufacturing. The researchers chemically modified liquid latexes to fabricate them printable and constructed a custom three-D printer with an embedded computer vision machine to print loyal, excessive-resolution beneficial properties of this excessive-efficiency materials.
“This mission represents the quintessential example of interdisciplinary study,” mentioned Timothy Lengthy, a professor of chemistry and a co-main investigator on this mission alongside with Christopher Williams, the L.S. Randolph Professor of mechanical engineering and meantime director of MII. “Neither of our labs would be in a suppose to produce this with out the a fashion of.”
This mission is a joint collaboration between Virginia Tech and Michelin North The United States by capacity of a Nationwide Science Foundation award aligned with the Grant Alternatives for Tutorial Liaison with Change program, which helps teamed study between academia and change. Fundamental beneficial properties of their initial outcomes are detailed in a journal article printed in ACS Utilized Materials & Interfaces.
Recent materials pattern in science
After unsuccessful attempts to synthesize a materials that would possibly maybe well well present the suitable molecular weight and mechanical properties, Phil Scott, a fifth-one year macromolecular science and engineering student within the Lengthy Compare Team, turned to industrial liquid latexes.
The researchers within the slay wished this materials in a solid three-D printed accumulate, but Scott first wanted to raise the chemical composition to allow it to print.
Scott bumped correct into a most indispensable narrate: liquid latex is amazingly fragile and difficult for chemists to alter.
“Latexes are in a suppose of Zen,” mentioned Viswanath Meenakshisundaram, a fifth-one year mechanical engineering Ph.D. student within the Salvage, Compare, and Education for Additive Manufacturing Systems Lab who collaborated with Scott. “Must you add something else to it, it’ll fully lose its balance and shatter out.”
Then, the chemists got right here up with a brand unusual idea: What if Scott constructed a scaffold, identical to those former in building building, spherical the latex particles to take care of them in keep? This means, the latex would possibly maybe well well again its enormous structure, and Scott would possibly maybe well well add photoinitiators and a fashion of compounds to the latex to enable three-D printing with ultraviolet (UV) gentle.
“When designing the scaffold, the ideal factor you prefer to fear about is balance of the entire lot,” Scott mentioned. “It took a fashion of reading, even stuff as classic as studying why colloids are right and the way colloidal balance works, but it completely became a in actuality fun narrate.”
Recent processing pattern in engineering
While Scott tinkered with the liquid latex, Meenakshisundaram had to settle out how to accurately print the resin. The researchers chose to expend a course of called vat photopolymerization, in which the printer makes expend of UV gentle to treatment, or harden, a viscous resin correct into a particular form.
Needing a printer capable of printing excessive-resolution beneficial properties throughout a enormous home, Meenakshisundaram constructed a brand unusual printer. He and Williams, his handbook, got right here up with the concept to scan the UV gentle throughout a enormous home, and in 2017, they filed a patent for the printer.
Even with the custom printer, the fluid latex particles triggered scattering outside of the projected UV gentle on the latex resin surface, which resulted in printing unsuitable facets, so Meenakshisundaram devised a 2nd unusual idea. He embedded a digital camera onto the printer to win a record of every vat of latex resin. Along with his custom algorithm, the machine is in a suppose to “glimpse” the UV gentle’s interplay on the resin surface and then robotically adjust the printing parameters to simply for the resin scattering to treatment correct the supposed form.
“The enormous-home scanning printer became a idea I had, and Viswanath made it into actuality briefly deny,” Williams mentioned. “Then Viswanath got right here up with the concept of embedding a digital camera, watching how the gentle interacts with the materials, and updating the printing parameters in line alongside with his code. That is what we need from our Ph.D. college students: We present a vision, and to boot they produce that and grow beyond as an self reliant researcher.”
Meenakshisundaram and Scott chanced on their closing three-D printed latex facets exhibited solid mechanical properties in a matrix identified as a semi-interpenetrating polymer network, which hadn’t been documented for elastomeric latexes within the prior literature.
“An interpenetrating polymer network is admire catching fish in a get dangle of,” Meenakshisundaram mentioned. “The scaffold provides it a form. When you put that within the oven, the water will evaporate, and the tightly coiled polymer chains can loosen up, unfold or circulation, and interpenetrate into the online.”
A molecules-to-manufacturing capacity
The unusual advances in every materials pattern and processing highlight the interdisciplinary atmosphere fostered between the two groups.
Lengthy and Williams every credited their counterpart’s ride for making the collective step forward imaginable.
“My philosophy is all these innovations are top probably achievable when you accomplice with of us which will probably be very a fashion of from you,” Lengthy mentioned.
The 2 professors mentioned three-D printed latex provides the conceptual framework for printing a fashion of unheard of materials from inflexible plastics to soft rubbers, which were unprintable till now.
“After I became a graduate student engaged on this skills, we were angry to construct up uncommon efficiency from the shapes shall we form, however the underlying assumption became we had to fabricate carry out with very uncomfortable materials,” Williams mentioned. “What’s been so absorbing about this discovery with Tim’s neighborhood is being in a suppose to push the boundary of what we assumed became the limit of a printed materials’s efficiency.”
More files:
Philip J. Scott et al. 3D Printing Latex: A Path to Complex Geometries of Excessive Molecular Weight Polymers, ACS Utilized Materials & Interfaces (2020). DOI: 10.1021/acsami.9b19986
Citation:
Researchers report three-D printed latex rubber step forward (2020, July 15)
retrieved 15 July 2020
from https://phys.org/files/2020-07-d-latex-rubber-step forward.html
This doc is field to copyright. Except for any handsome dealing for the motive of non-public look or study, no
half would possibly maybe well well be reproduced with out the written permission. The affirm material is equipped for files beneficial properties top probably.